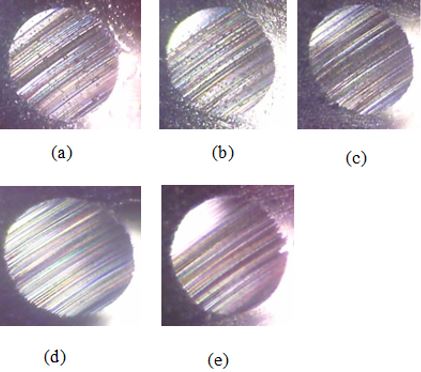
Figure 4: Optical microscopic images of worn-out surfaces of balls under formulated nano lubricant (a) PBA (b) PBA1 (c) PBA2 (d) PBA3 (e) PBA4
Optical microscopic images of ball after experimentation were presented in figure 4. Figure 4(a)-(e) showed the optical images of balls under lubrication of bitter almond oil and oil containing 0.01, 0.02, 0.03 and 0.04 vol. fraction of nanoparticles, respectively. The AWSD was measured after taking the optical microscopic images. The optimum concentration was 0.02 vol fraction of nanoparticles.
Conclusion
Bitter almonds oil-based nano lubricant containing TiO2 nanoparticles and Triton X-100 was successfully formulated. Four different volume fractions of nanoparticles (0.01, 0.02, 0.03, and 0.04) used for nano lubricant formulation and the ratio of TiO2 nanoparticles and Triton X-100 is 2:1. The tribological investigation of formulated Bitte almond oil-based nano lubricant on Four ball tribotester using ASTM 4172B. Bitter almonds oils containing 0.02 vol. fraction nanoparticles showed minimum average wear scar diameter of 519 µm and 0.02 coefficient of friction. Bitter almond oil is a non-edible oil and it can be recommended for the lubricant formulation with TiO2 nanoparticles.
References
1. Karmakar G, Ghosh P, & Sharma BK. (2017). Chemically modifying vegetable oils to prepare green lubricants.Lubricants, 5(4), 44.
2. Salimon, N. Salih, & E. Yousif. (2010). Biolubricants: raw materials, chemical modifications and environmental benefits. Eur. J. Lipid Sci. Technol., 112(5), 519–530. doi: 10.1002/ejlt.200900205.
3. Mandaković , & Novina B. (2015). Trends, demands and paradoxes of lubricant micro markets such as Croatia and the surrounding countries. Croatian Society for Fuels and Lubricants.
4. Sevim Z Erhan, & Svajus Asadauskas. (2000). Lubricant basestocks from vegetable oils. Industrial Crops and Products, 11(2–3), 277-282.
5. Ettefaghi, et al. (2013). Preparation and thermal properties of oil-based nanofluid from multi-walled carbon nanotubes and engine oil as..., International Communications in Heat and Mass Transfer.
6. Asrul, N. W. M. Zulkifli, H. H. Masjuki, & M. A. Kalam. (2013). Tribological properties and lubricant mechanism of nanoparticle in engine oil. Procedia Eng., 68, pp. 320–325. DOI: 10.1016/j.proeng.2013.12.186.
7. Arumugam, & G. Sriram. (2014). Synthesis and characterization of rapeseed oil bio-lubricant dispersed with nano copper oxide: Its effect on wear and frictional behavior of piston ring–cylinder liner combination. Proc. Inst. Mech. Eng. Part J J. Eng. Tribol., 228(11), pp. 1308–1318. doi: 10.1177/1350650114535384.
8. Dinesh, M. J. G. Prasad, R. R. Kumar, N. J. Santharaj, J. Santhip, & A. S. A. Raaj. (2016). Investigation of tribological and thermophysical properties of engine oil containing nano additives. Mater. Today Proc., 3(1), pp. 45–53. doi: 10.1016/j.matpr.2016.01.120.
9. Cortes, & J. A. Ortega. (2019). Evaluating the rheological and tribological behaviors of coconut oil modified with nanoparticles as lubricant additives. Lubricants, 7(9), 76. doi: 10.3390/lubricants7090076.
10. Cortes, K. Sanchez, R. Gonzalez, M. Alcoutlabi, & J. A. Ortega. (2020). The performance of SiO2 and TiO2 nanoparticles as lubricant additives in sunflower oil. Lubricants, 8(1), 10. doi: 10.3390/lubricants8010010.
11. Opia, A. H. M. Kameil, Z. H. C. Daud, C. Mamah, M. I. Izmi, & A. B. A. Rahim. (2020). Tribological properties enhancement through organic carbon nanotubes as nanoparticle additives in boundary lubrication conditions. pp. 16.
12. M. Liñeira del Río, E. R. López, F. García, & J. Fernández. (2021). Tribological synergies among chemical-modified graphene oxide nanomaterials and a phosphonium ionic liquid as additives of a biolubricant. J. Mol. Liq., 336, 116885.